Crafting Your Perfect Wave Rider: A Guide to Surfboard Building
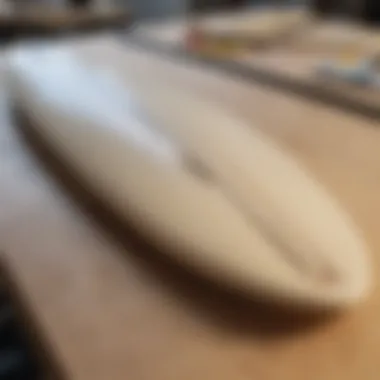
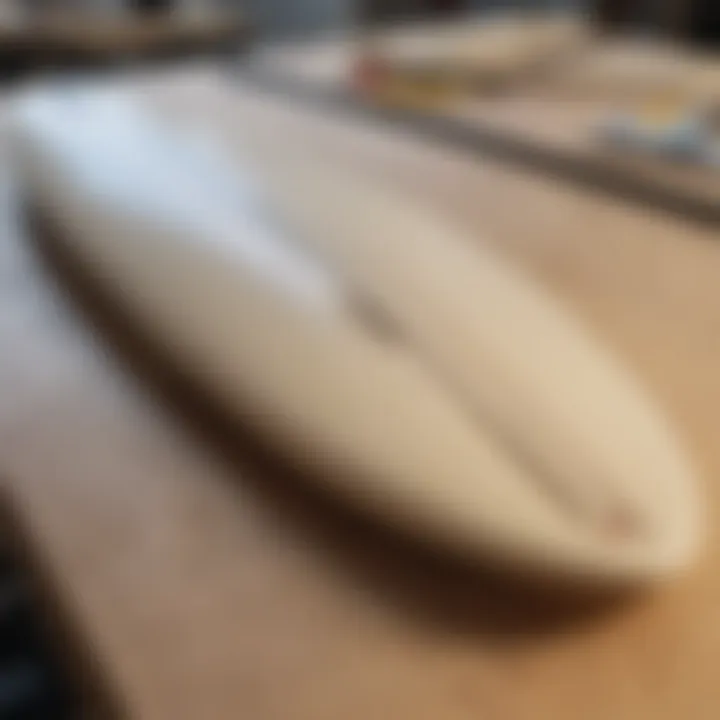
Intro
Building a surfboard can be likened to cooking a fine meal; it’s not just a task but a creative process that combines art and science. For many, surfing is more than just a sport. It's a lifestyle steeped in culture and passion, and crafting your own board is the ultimate expression of that commitment. Let’s face it, there’s a certain magic about riding waves on a board you've shaped with your own hands. Not only do you get an instrument tailored to your style, but it carries a piece of you into the surf.
In this exploration, we’ll dive into the nuts and bolts of surfboard construction — from materials choice to issue of sustainability. Whether you're looking to build a simple board for casual summer afternoons or a high-performance model for those gnarly big swells, this guide aims to equip you with the knowledge you need. Grab your toolkit and let’s get started.
Tips and Techniques
Beginner Tips for Watersports
Starting out in surfboard building can indeed feel like learning to bake bread from scratch — daunting yet rewarding. A few foundational tips can help make the journey smoother:
- Research your boards: Familiarize yourself with different surfboard types and their designs. Foam boards, longboards, shortboards, and hybrids each have unique characteristics. Take a surf shop tour or sift through forums on Reddit to gather insights from seasoned surfers.
- Get hands-on experience: There's no better way to learn than to dive in. Consider attending workshops offered by local surfboard builders or schools. Practical exposure can be invaluable, boosting your confidence and skill with every attempt.
- Be patient: Like anything worthy, mastering surfboard construction takes time. Embrace mistakes as part of learning. Even seasoned builders still modify and refine their techniques.
Advanced Techniques for Mastery
Once you’ve got your sea legs, there’s a wealth of techniques that can elevate your surfboard building skills to new heights:
- Precision shaping: Perfecting the contour of your board can hugely impact its handling. Invest time learning how to use a planer to adjust thickness and achieve intended rocker profiles.
- Fin placement: Consider experimenting with different fin setups and placements. Depending on your desired ride, you might prefer a thruster setup for stability or a quad for speed and maneuverability.
- Resin tinting and artwork: Adding color and art can make your board truly personal. Explore various resin techniques, including marbling or metallic blends, to create a board that stands out.
Safety and Gear
Essential Safety Practices
Working with certain materials and tools can pose risks if proper safety protocols are not observed. Be mindful of these essential practices:
- Ventilate your workspace: Many materials, like epoxy resin, release harmful fumes. Ensure your workspace is well-ventilated to avoid harmful exposure.
- Wear protective gear: Safety goggles, gloves, and masks are non-negotiable. They prevent inhalation of dust and exposure to chemicals.
- Keep a first-aid kit nearby: Always have a well-stocked first-aid kit ready. Minor cuts from tools or slips are common and being prepared can save the day.
Gear Reviews and Recommendations
When gearing up for board building, a few items stand out that can significantly improve your experience:
- Surfboard Shaping Tools: Invest in a quality foam planer — look for brands like Surform, which offers fine control and efficiency.
- Resin Kits: Consider using West System Epoxy, as it’s known for its clarity and strength, ensuring a stellar finish on your board.
- Safety Equipment: Don’t skimp on safety. Get high-quality respirators that filter volatile organic compounds (VOCs) to keep your lungs happy.
"The best surfer out there is the one having the most fun." — Unknown
Intro to Surfboard Building
Building a surfboard is not only about slapping some foam and fiberglass together; it’s a nuanced craft that carries a rich history and a personal touch for every surf enthusiast out there. Understanding the importance of customizing a surfboard, along with its historical background, lays the foundation of this extraordinary journey. For athletes, coaches, and anyone keen on surfing, recognizing the significance of surfboard craftsmanship is crucial—it connects the surfer to the board in ways that can profoundly enhance performance and enjoyment.
Historical Context
Diving into the historical context of surfboard building reveals a fascinating evolution. The roots of surfboarding can be traced back to ancient Polynesian culture, where the first wave riders crafted boards from solid pieces of wood. These early surfers understood the relationship between board shape, size, and water dynamics long before modern technology entered the scene. Fast forward to the 20th century, and you see a surge in innovation.
In the 1950s, surf culture took off, and builders began experimenting with new materials. The introduction of foam cores and fiberglass revolutionized surfboard design, allowing for lighter and more durable boards. This led to different shapes and sizes tailored for speed and maneuverability. Names like Hobie Alter and Donald Takayama became legends, pushing boundaries in surfboard design. Today, surfboard building is a blend of art and science, where historical insights coexist with cutting-edge technology.
Importance of Customization
Customization is key when it comes to surfboards. A one-size-fits-all approach simply doesn't cut it in the world of surfing. Each surfer's style, skill level, and preferred conditions dictate what they need from their board. What might work for a seasoned pro tackling serious waves won't suit a beginner catching their first break.
- Performance Optimization: Custom boards allow for precision adjustments—tail shape, width, and rocker can all be tailored to match your surfing style.
- Enhanced Comfort and Fit: A board that feels tailored to your size and weight is essential for comfort. This ‘custom fit’ can make all the difference in how confident you feel on the water.
- Expression of Personality: A custom board shows off not just your surfing needs but also your unique style—color schemes, artwork, and shapes can reflect who you are.
- Connection to the Craft: Taking part in the building process fosters a deeper connection with the surfboard, making each ride feel even more rewarding.
"Custom surfboards breathe personality into the wave rider, crafting not just a tool for performance, but a piece of art that resonates with one's spirit."
Understanding Surfboard Anatomy
When embarking on the journey of crafting your own surfboard, a thorough understanding of its anatomy serves as the backbone of the process. The anatomy of a surfboard dictates not just its appearance but fundamentally influences its functionality in the waves. A deeper dive into the structure enables aspiring wave riders to tailor their boards to their specific needs, ensuring that each ride is as dynamic as the ocean itself.
Not every surfboard is born equal; different components work in combination to offer unique advantages, fitting certain types of waves and rider styles. A precise knowledge of each part not only aids in the building process but also informs how adjustments can optimize performance. Familiarity with the anatomy allows you to get the most out of your equipment, making it a paramount aspect of this article.
Parts of a Surfboard
Understanding the parts of a surfboard is akin to knowing the anatomy of any finely tuned machine. Each element, from the tail to the nose, contributes to how the board handles both in and out of the water. Here’s a breakdown of the key components:
- Nose: The front of the surfboard is often rounded or pointed, affecting paddling and wave engagement. A wider nose offers increased buoyancy while a pointed shape provides better slicing through the water.
- Tail: Depending on its shape—square, round, or pintail—the tail plays a crucial role in maneuverability and speed. A wider tail can provide more lift, impacting how the board responds in turns.
- Rails: The edges around the surfboard, known as rails, influence how the board cuts through water. A thinner rail will create less drag, whereas a thicker rail offers better stability in turbulent waters.
- Bottom Contours: A big player in how fast and fluid a surfboard can glide over a wave. Concave shapes can increase lift and speed, whereas flat bottoms provide stability.
- Fins: These are the small, yet mighty, appendages that help with control and stability. Different fin setups—thruster, quad, or single—can dramatically change how a board rides.
Learning about these components provides essential insights into how they work individually and collectively. A nuanced appreciation for the anatomy helps surfers experiment with designs to find the combination that feels just right under their feet.
How Design Influences Performance
The design of a surfboard often serves as the silent partner in a surfer's performance. It kicks into gear in the most critical moments, dictating the feel and maneuverability of the board. Design elements such as shape, size, and rail configuration all play pivotal roles in determining how a surfboard interacts with ocean swells.
- Length and Width: Longer boards generally offer greater stability and ease of paddling, making them suitable for beginners or larger waves. Shorter boards excel in quick turns and responsiveness, ideal for advanced surfers aiming to cut through smaller swells.
- Volume: The amount of buoyancy directly correlates to the surfer's ability to float and paddle effectively. A higher volume board will be easier to manage but may sacrifice some speed compared to its thinner counterparts.
- Rocker: This refers to the curve of a surfboard from nose to tail. A pronounced rocker can enhance control, particularly in steep waves, while a flat rocker provides better speed on less powerful swells.
Design impacts not just physical performance but also psychological confidence. Knowing one’s board inside and out can make or break a session. As one might reflect, a board that feels right inspires the mind to push limits. Ultimately, effective design tailored to individual riding style reflects a deeper understanding, ensuring every ride feels connected, fluid, and unlocked.
"A well-designed surfboard becomes an extension of the surfer, turning each ride into a moment of grace and motion."
Materials Used in Surfboard Construction
When it comes to surfboard construction, the materials selected are akin to the notes that build a symphony. Each element plays its unique role, establishing the performance, durability, and aesthetics of the final board. It's essential to understand that the right combination can make the difference between a board that feels like a dream and one that leaves you struggling to catch waves. Thus, knowing the type of materials can enhance not just the surfing experience, but also contribute to a more sustainable approach to building.
Foam Cores
At the heart of every surfboard lies the foam core. This component serves as the foundation, giving both buoyancy and structure. The most common type of foam used is polyurethane, but there's also a growing preference for extruded polystyrene and carbon fiber alternatives. Each material offers different density and flexibility, which can significantly impact how the board performs in the water.
- Polyurethane Foam: This is the classic choice for many surfers. It’s easy to shape, light, and provides a nice balance between stiffness and flexibility.
- Extruded Polystyrene: While a bit pricier, this foam is highly regarded for its water resistance. It can be an excellent option for those who want a longer-lasting board.
- Carbon Fiber: Going mainstream, carbon fiber foam cores are desired for their strength-to-weight ratio. Though it’s more commonly used in high-performance boards, it’s gaining traction among builders keen on innovative designs.
Choosing the right foam for your surfboard can direct influence how it rides. A thinner core may allow for better maneuverability, while a thicker core can provide more stability, especially in larger waves.
Fiberglass Cloth
Once the foam core is shaped, it’s time to reinforce it with fiberglass. This material acts like the tough skin of the board. Fiberglass cloth is renowned for its durability and resistance to wear and tear. When selecting the right fiberglass cloth, there are a few important points to consider:
- Weight: The weight of the fiberglass can change the board’s performance. Lighter cloths typically allow for quicker turns while heavier cloths can increase durability.
- Weave Type: The weave of the fiberglass can affect the overall feel of the board. A tighter weave can lend extra strength, whereas a looser weave might add flexibility, tailored for surfers who prefer a more fluid ride.
- Multiple Layers: Most builders will layer the fiberglass to obtain a balance of strength and flexibility. More layers can offer more protection but also adds weight, requiring a judicious approach when determining how many layers to use.
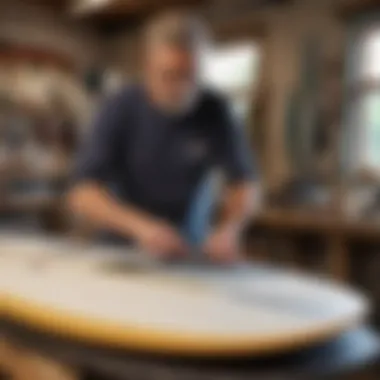
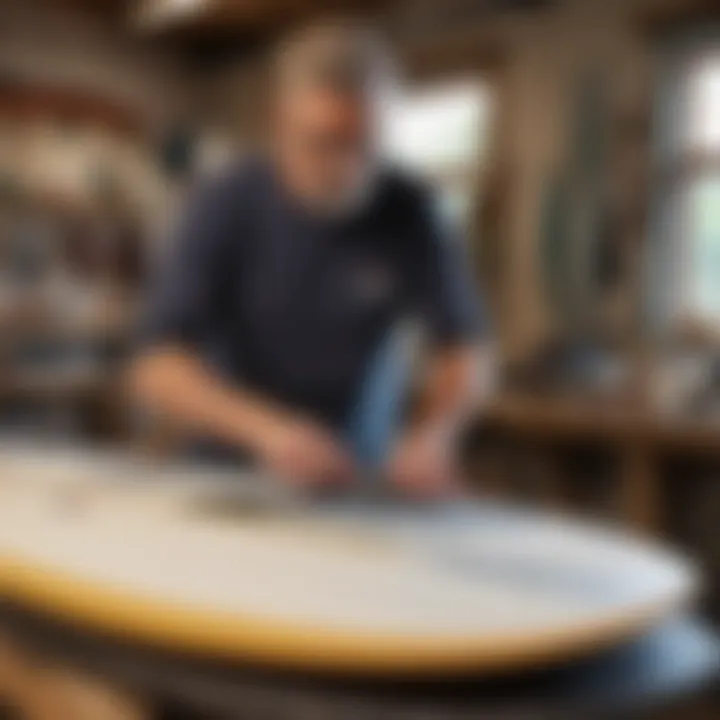
Incorporating fiberglass into the build is crucial. It not only protects the foam core but also affects water flow on the surface, which can enhance or hamper speed and maneuverability.
Resins and Coatings
The final touch in surfboard construction involves resins and coatings. They seal in the fiberglass and add a finishing layer that can influence both the look and longevity of the board. Epoxy and polyester are the two main types of resin.
- Epoxy Resins: Known for their strength and durability, epoxy resins are less harmful to the environment and produce a lighter board. Despite being more expensive, they often justify the cost for those seeking these benefits.
- Polyester Resins: The cheaper alternative, polyester resins have been the go-to in the industry for decades. However, they can be less durable and more corrosive to the environment.
Once the resin is applied, a clear coat is usually added to protect the surface from UV rays and water damage. A gloss finish not only enhances aesthetics but contributes to water dispersion, which can lead to smoother rides.
Managing the environmental impacts along with your personal choices regarding materials can significantly influence the sustainability of the surfboard you create. So diving into this subject not only concerns the structure of the board but also poses crucial questions about longevity, efficiency, and ecological responsibility.
"The essence of a surfboard lies not in its shape, but in the materials and the stories they weave into every wave you ride."
Understanding these elements is critical for any aspiring surfboard builder or enthusiast. With a solid grasp of materials, one can tailor the board to suit individual style, aspirations and the waves they seek.
Essential Tools for Building a Surfboard
Building a surfboard isn’t just about a keen eye for design and a love for the waves; it’s also heavily reliant on the right set of tools. The essential tools not only streamline the construction process but also ensure precision and quality in the final product. With the right equipment at hand, any aspiring shaper can turn a simple block of foam into a masterpiece that rides the waves beautifully. This section explores the key tools necessary for surfboard construction and the attributes that make them indispensable.
Cutting Tools
When it comes to cutting tools, accuracy is key. The first step in building your surfboard involves slicing the foam into the desired shape and size. Commonly used cutting tools include:
- Polyurethane Foam Cutter: This is an ideal choice for initial cuts. It features a heated wire that slices through foam effortlessly, reducing the risk of rough edges that can affect precision.
- Hand Saw: While somewhat traditional, a hand saw can offer control for those intricate cuts that require a careful hand.
- Utility Knife: Great for smaller adjustments, this tool allows for detailed trimming and refinement once the main structure is established.
Cutting tools must be handled with care, ensuring that safety is top of mind. Sharp edges can lead to accidents, so proper handling techniques and protective gear are always recommended. Cutting tools are the backbone of the surfboard-building process, making it vital to select the right ones for your needs.
Shaping Tools
Once the board is cut to the core size, it's time for shaping. This stage is where the art really comes into play, as the shaper can start giving life to the board's intended performance characteristics. Key shaping tools include:
- Planers: These are indispensable for quickly removing foam to reach the desired outline and thickness. Electric planers can save time and energy, though manual versions give a greater feel of control.
- Rasp and Sanding Blocks: Perfect for final details, these tools help in fine-tuning curves and smoothing the surface. A good rasp will help carve out channels and contours with ease, allowing for finesse in design.
- Templates: While not a toolper se, templates allow shapers to ensure consistent dimensions throughout the shaping process. They can be made from wood or even cardboard and are crucial to achieving balanced contours.
Shaping tools define the physical feel and performance of the surfboard, ultimately influencing how it responds in the water. A skilled shaper knows that taking the time to get this right pays off in the ride.
Finishing Tools
The finishing stage is where the surfboard shines, quite literally. After shaping, the board needs to boast a smooth finish, contributing not only to aesthetics but also to hydrodynamics. Finishing tools include:
- Orbital Sander: This tool speeds up the sanding process while ensuring an even surface without the risk of creating flat spots. It's particularly reliable for large surfaces.
- Detail Sanders: For those tight spots and rounded edges, a detail sander can make an enormous difference, allowing the shaper to reach every nook and cranny effectively.
- Polishing Pads: These provide the final touch, enhancing the gloss and ensuring that the visual appeal matches the performance quality of the board.
Navigating the variety of tools available allows shapers to maintain their unique style while ensuring their board meets quality standards. The right finishing tools not only enhance appearance but they also play a significant role in performance enhancement on the water.
"Having the right tools is half the battle in surfboard crafting — they turn a vision into reality."
Equipping yourself with the right assortment of cutting, shaping, and finishing tools is crucial for anyone looking to dive into surfboard building. Each tool adds a layer of precision and professionalism that’s needed to truly craft a wave rider that performs as well as it looks.
Safety Precautions During the Building Process
When it comes to surfboard building, safety precautions are anything but a side note. Engaging in this craft not only requires technical skills but also a strong commitment to safety as well. The process can expose builders to various hazards ranging from harmful dust particles to chemical fumes. Implementing safety measures not just protects the individual but also ensures a smooth workflow and enhances the overall experience. Neglecting these aspects can lead to unwelcome consequences, such as injuries or long-term health issues.
Protective Gear
Dressing for success is not simply a colloquial expression, it's a necessity in the realm of surfboard crafting. Protective gear plays a critical role in minimizing risks. Here are essential elements of protective gear one should consider:
- Safety Goggles: Always keep your eyes protected from dust and particles while sanding or cutting. A moment of carelessness can lead to a nasty injury.
- Respirators or Masks: Good air quality is crucial. Make sure to have a well-fitted respirator to prevent inhalation of fine dust or harmful fumes that arise from resin applications.
- Gloves: Nitrile gloves can shield your hands from skin irritation caused by materials like fiberglass and epoxies.
- Ear Protection: If you are working with loud cutting tools, invest in quality earplugs or earmuffs to protect your hearing.
The importance of these items can’t be overstated—without proper gear, builders can find themselves in harm's way much quicker than they’d expect.
Ventilation and Workspace Safety
The workspace should be a haven for creativity, but it also needs to be safe. Proper ventilation is crucial when working with materials that can emit fumes. An enclosed space with a poor air flow can turn into a health hazard faster than you can say "surfboard." Here are a few aspects to consider:
- Proper Airflow: Ensure that there is adequate airflow in your workspace. Open windows or use exhaust fans to help facilitate this.
- Dedicated Workstations: Set up distinct areas for cutting, shaping, and glassing to minimize cross-contamination of materials. Not mixing composite materials helps avoid chemical reactions that could pose risk.
- Orderliness: Maintain a tidy workspace. Cluttered benches can lead to accidents, making it difficult to find tools and hazardous if you trip over misplaced items.
"Safety doesn’t happen by accident; it’s about taking deliberate steps to protect yourself and promoting a culture of awareness."
Keeping safety top-of-mind not only makes the building process smoother but fosters a creative environment where enthusiasts can work confidently without fear of accidents. Making sure protective gear is worn and that the workspace is safe can transform the surfboard construction from a tricky task to a fulfilling endeavor, where the excitement of crafting your personalized ride can be combined with the joy of knowing you are acting responsibly.
Design and Shaping Your Surfboard
Creating the perfect surfboard is a delicate blend of art and science. Every wave rider has unique preferences, and understanding how to design and shape your surfboard can greatly influence your surf experience. This section delves into the key aspects of surfboard design, emphasizing how the right choices can enhance performance and make your time on the water more enjoyable.
Selecting the Right Template
Choosing a template is akin to picking a blueprint for a house; it sets the foundation for everything that follows. The template not only defines the surfboard’s outline but also influences its volume, rocker, and ultimately, its handling in the water.
When selecting a template, consider the type of waves you plan to ride. For instance, short boards are designed for quicker turns in steep, powerful waves, while long boards provide stability and ease of paddling in smaller conditions. Some points to ponder:
- Wave Conditions: Understand your typical surf spots. Do they have a steep break or a gentle slope?
- Skill Level: Newer surfers may benefit from a wider board for better stability.
- Personal Style: Think about how you like to ride. Fast, agile maneuvers, or smooth, flowing lines?
Using software like Shaper3D can make selecting the right template more visual and straightforward, allowing one to experiment digitally before committing.
Techniques for Shaping Foam
The shaping process is where creativity meets technical skill. Shaping foam involves slicing, sanding, and molding the blank into something wondrous. Familiarize yourself with some effective techniques:
- Planing: Using a planer allows for the removal of excess material quickly. This step is crucial in achieving the desired thickness and curvature of the board.
- Sanding: Hand sanding plays a vital role in shaping the nuances. The curve of the rails, the contours of the bottom, and the rocker can all be fine-tuned during this stage. A smooth finish not only feels better but enhances the flow through the water.
- Profiling: Crafting the specific outline of the board’s nose and tail is key. The profile affects how the board handles waves, with pulled-in tails creating sharper turns and wider noses allowing for more stability.
- Testing: After shaping, it's wise to conduct mock tests to see how the board performs on land before taking it to the surf. Adjustments can be made at this stage, ensuring your board feels right.
A well-shaped foam blank will serve as the backbone of your board, influencing how it slices through waves and how it feels beneath your feet.
"The magic of shaping foam is about transforming a lifeless blank into a vessel of expression, poised to catch waves and carve paths through the ocean."
In essence, design and shaping your surfboard are about personal expression blended with efficient performance. Your choices during this stage set the tone for every ride to come.
Fin Placement and Setup

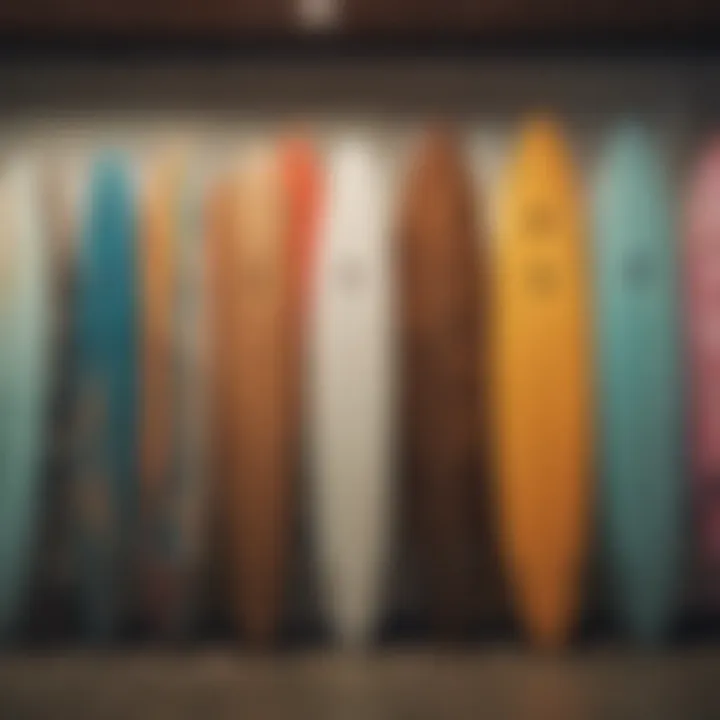
In the realm of surfboard design, fin placement and setup play a pivotal role in determining how a board performs in the water. This section delves into the significance of choosing the right fins and arranging them in a manner that optimizes your surfing experience. Proper fin placement can influence factors such as stability, control, and turning ability, crucial for every surfer from novices to seasoned wave riders.
Types of Fins
Fin types come in various shapes and sizes, each designed to cater to different surfing styles and wave conditions. Understanding these types can significantly enhance your tuning process:
- Thruster Fins: Typically consists of three fins; it offers a perfect balance of speed and maneuverability, making it a popular choice for a variety of surf conditions.
- Quads: Featuring four fins, this setup provides increased speed and holds in fast, hollow waves. Ideal for surfers looking for an ultra-smooth ride.
- Single Fin: A favorite from the retro days, the single fin setup lends itself well to longboards and cruisers, allowing for graceful turns and a flowing style.
- Twin Fins: Two fins provide quick turns and speed, primarily useful for surfing smaller, softer waves.
Each fin type comes with its own set of characteristics, and realizing those nuances can enable a surfer to match their board's capabilities with the surf conditions.
Adjusting Fin Configuration for Performance
Fin configuration can dramatically alter how a surfboard reacts on the waves. Here are a few considerations to keep in mind when tweaking your fin setup:
- Angle of the Fins: The angle at which fins are installed (also known as toe-in) can enhance or dampen responsiveness. Slightly angled fins result in better grip, while straight fins can provide more speed.
- Fin Height and Width: Taller fins offer better hold in steep waves, while shorter fins can help in maintaining speed and executing quick turns.
- Spread Between Fins: The distance between fins affects stability. Wider spreads typically increase stability, while tighter setups can improve maneuverability.
Moreover, for those looking to find the sweet spot of performance, experimenting with fin placements and configurations can yield insights that transform your ride. Remember, there’s no one-size-fits-all when it comes to fin setup; it should resonate with personal style and nearly every wave encounter.
"The right fin setup can turn your average ride into an exhilarating experience, amplifying your control and enjoyment while surfing."
Taking the time to explore different fin types and adjusting configurations offers an opportunity to personalize your surfboard uniquely. The process might be intricate, but with patience and methodical trial-and-error, every wave can become a new adventure.
Resin Application and Glassing
When it comes to building a surfboard, resin application and glassing are pivotal stages that determine not only the durability of the board but also its overall performance. This part of the process seals the foam core and adds strength, ensuring that your surfboard can withstand the rigors of the waves. Understanding the nuances of resin types, application techniques, and glassing methods will equip you with the knowledge needed to create a robust and reliable wave rider.
Mixing and Applying Epoxy Resins
Epoxy resins are becoming the go-to choice for modern surfboard construction. They are generally more durable and user-friendly compared to traditional polyester resins. The key to achieving a solid bond during the resin application lies in the mixing ratio, which is typically specified by the manufacturer. Generally, a 2:1 ratio of resin to hardener is common for epoxy systems.
- Preparation: Before mixing, ensure your work area is well-ventilated. Gather all materials, including your mixing bucket, stirring stick, and protective gear such as gloves and a mask.
- Mixing: Pour the measured resin into the mixing bucket. Add the hardener slowly, mixing with a stirring stick. Aim for a consistent blend that is free from bubbles. This step is crucial; an improper mix can lead to weak points in the final product.
- Application: Once mixed, apply the resin evenly over the board using a squeegee or brush. Start from one end and move to the other, ensuring you cover all areas without leaving any dry spots. It’s vital to work efficiently in this stage as epoxy cures at a set pace.
- Curing: Allow the resin to cure as per the manufacturer’s instructions, ideally in a dust-free environment. This stage is where the resin hardens, providing a sturdy surface over the foam core.
Laminating Fiberglass Cloth
Laminating fiberglass cloth onto your surfboard molds the structure and adds an extra layer of protection. This process enhances the board’s stiffness and resistance to impact. The right cloth and technique can significantly influence how your board performs in the water.
- Selecting Fiberglass Cloth: Fiberglass comes in various weights and weaves. A heavier cloth offers more durability, while lighter options enhance flexibility. For most surfboards, a 4 oz. or 6 oz. cloth strikes a nice balance between strength and flexibility.
- Cutting the Cloth: Measure your board dimensions and carefully cut the fiberglass cloth to size. Always allow for a little extra material to wrap around the edges; this will help reinforce seams when the resin is applied.
- Application Process: After the resin has been applied, place the fiberglass cloth over your board. Start smoothing it down gently but firmly, avoiding wrinkles or bubbles. Using a brush or roller, apply a second layer of resin over the cloth, ensuring it saturates completely.
- Final Curing: Similar to the first resin application, let this layer cure thoroughly. The glass itself serves not just as a protective layer but also plays a crucial role in the board's buoyancy and agility in water.
"Well executed resin application and glassing not only extend the life of your surfboard but also enhance its aesthetic appeal. A glossy finish is not just for looks; it reduces drag, allowing for better performance on the waves."
Finishing Touches: Sanding and Polishing
The process of building a surfboard doesn’t end once the epoxy has cured. The final stages of sanding and polishing play a critical role in shaping both the board's performance and aesthetic appeal. Finishing touches are not merely about making the surfboard look good; they directly impact how well the board moves through the water. A smooth surface reduces drag, allowing the rider to cut cleanly through the waves. Additionally, a well-polished board resonates with the personal touch that every surfer cherishes.
Techniques for Even Sanding
Achieving a perfectly sanded surfboard involves more than just picking up a sander and going at it. It’s an art that requires patience and precision. Here are the essential techniques to ensure even sanding:
- Start with Coarse Grit: Begin with a coarse grit sandpaper, like 80 or 100 grit. This helps in removing excess resin and leveling the surface. Be careful not to sand too deep into the foam core, as it can damage the integrity of the board.
- Move in Circular Motions: Always sand in circular motions rather than back and forth. This technique helps to avoid creating flat spots and enhances the evenness of the surface.
- Use a Block or Tool: For flat areas, utilize a sanding block to maintain even pressure. This prevents creating dips or bumps. For curved sections, consider using flexible sanding pads that can conform to your board's shape.
- Progressively Finer Grits: Gradually move to finer grits, finishing with 220 to 400 grit to achieve a smooth finish. This step-wise approach is crucial; skipping grits can lead to visible scratch marks in the final image.
Achieving a Glossy Finish
A glossy finish is not just the cherry on top; it enhances more than the aesthetics of your surfboard. Here are way to reach that polished shine:
- Buffing Compound: After sanding, apply a good-quality buffing compound with a soft cloth. This step is essential in eliminating fine scratches that might have been left behind.
- Polishing Machine: If available, use a polishing machine designed for epoxy surfaces. This can save a lot of elbow grease and give a more uniform glossy finish compared to manual buffing.
- Layering: Consider adding a clear coat after the final sanding. It should be of high quality to prevent cloudiness over time and maintain the board's vibrance. Allow ample curing time between coats to avoid bubbles or imperfections.
- Final Inspection: Once the glossy finish has been achieved, inspect the board under bright light. Any small imperfections that are spotted can easily be fixed with a bit more sanding and buffing.
Finishing touches may seem minor, but they genuinely can make or break your surfboard's performance and visual charm.
Taking the time to ensure that these final steps are properly executed pays off immensely. A meticulously sanded and polished surfboard not only becomes a personal statement for its owner but also elevates the overall surfing experience. Whether you are taking on small beach breaks or huge swells, your board’s performance largely depends on these finishing touches.
Environmental Considerations in Surfboard Building
In today’s surfing culture, there’s a growing awareness of how our choices influence the environment. Crafting surfboards is no longer just about hitting the right waves; it also means paying attention to the materials and methods involved in the shaping process. Making conscious decisions in surfboard building can lead to a more sustainable future for our oceans and the sport we love. This section delves into critical environmental considerations in surfboard building, highlighting sustainable practices and innovations that every builder should consider.
Sustainable Materials
One of the cornerstones in reducing the environmental impact of surfboard construction is the selection of sustainable materials. Traditional surfboards are constructed primarily using polyurethane foam, fiberglass, and polyester resin. These materials not only come with a hefty carbon footprint due to their production processes, but they also pose environmental hazards in terms of chemical emissions and waste.
The shift towards eco-friendly options has led to the introduction of materials such as bio-epoxy resins, which are derived from renewable resources and employ a process that generates fewer carbon emissions. Here are some sustainable alternatives:
- EPS Foam: Expanded Polystyrene foam is lighter and generates fewer pollutants during production compared to polyurethane.
- Natural Fibers: Some surfboard builders are experimenting with hemp or bamboo fibers for reinforcement.
- Recycled Materials: Using reclaimed materials like old boards or upcycled plastics helps reduce the demand for new resources.
Shifting focus to these materials doesn’t just lessen the environmental impact; it also offers performance benefits, influencing buoyancy and flex. Builders who embrace these sustainable choices not only contribute to a healthier planet but also tap into a more innovative market that values eco-friendliness.
Minimizing Waste in the Building Process
Another crucial aspect of environmentally considerate surfboard building is waste management. The surfboard manufacturing process can generate a substantial amount of off-cuts and excess material. Recognizing this, builders are finding creative ways to minimize waste and maintain efficiency, ensuring that every bit of resource is utilized. Here are a few strategies that can help:
- Precision Shaping Techniques: Investing time in better techniques can reduce off-cuts. Precise measurements and templates can prevent excess material loss.
- Off-Cut Reuse: Instead of discarding leftover foam, consider using it for small projects or repairs.
- Recycling Programs: Many communities encourage builders to recycle their surfboard materials, giving waste a second life.
By prioritizing waste reduction strategies, surfboard creators not only lower their impact on the environment but also foster a culture of sustainability within the surfing community, setting a solid example for future generations.
"Innovations in sustainable materials and waste management can redefine the surfboard building process and significantly lessen its impact on our planet."
The need for sustainable building practices is more pressing than ever. With the right materials and strategies, creating surfboards that ride the waves need not come at the expense of our environment.
Testing Your Surfboard
Testing your surfboard plays a crucial role in ensuring that all your hard work crafting it will come to fruition in the water. Some may think of this step as an afterthought, but it’s actually where theory meets practice. When you build a surfboard, you're not just shaping foam and layering fiberglass; you’re tailoring a unique experience to suit your style, skill level, and the types of waves you ride. Effective testing can reveal whether your surfboard lives up to those carefully laid plans and personal touches.
When hitting the waves, the right adjustments can make a world of difference in performance. A surfboard that feels great on the workbench may not fare well out in the ocean. The advantages of testing your board extend beyond performance indicators. You can also identify whether the design choices will truly enhance your surfing experience and refine your approach towards future builds, learning from each ride.
Water Testing Procedures
Once your surfboard is complete, venturing out into the ocean is the next big step. Before you jump on your new creation, there’s a recommended process for water testing that ensures everything is in order:
- Initial Inspection: Check the board for any visible defects like cracks or bubbles. It’s essential to spot any issues before putting the board to the test.
- Balance Test: Before paddling out, place your board on the water. Make sure it floats evenly. This checks the buoyancy and helps gauge whether the foam core is functioning properly.
- Paddle Test: Traverse through the water—this will help you assess how the board moves. If it feels heavy or turns sluggish, it might not be the right fit for you.
- Ride Test: This is where the excitement lies. Take it for a wave or two to experience how well it glides and maneuvers. Pay attention to how it reacts to your weight shifting and paddling technique.
- Evaluate: After the ride, take a moment to reflect. Do you feel comfortable? Is it responding to your commands like you imagined?
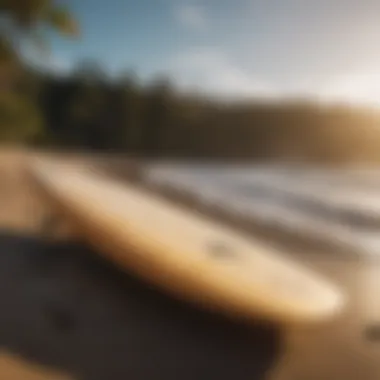
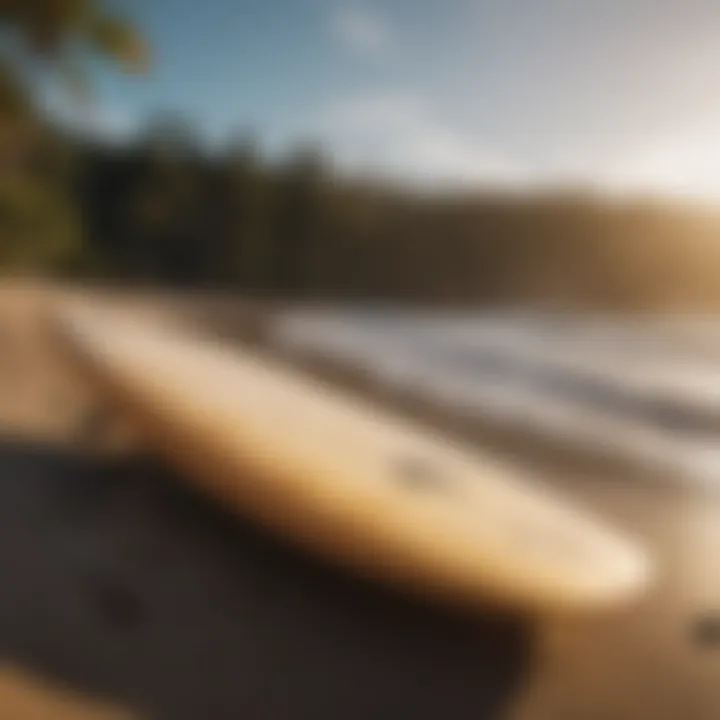
This process may feel a bit tedious, but each step gives you critical insight into your surfboard’s performance.
Comparing with Existing Boards
To further analyze the effectiveness of your newly crafted surfboard, comparing it with your existing boards offers vital points of reference. Keep in mind:
- Performance Metrics: How does your new board handle compared to others? Look for differences in speed, maneuverability, and stability.
- Feel and Comfort: Personal satisfaction is subjective. Pay close attention to how each board feels under your feet. A well-crafted board should feel like a natural extension of your body.
- Wave Type Compatibility: Match your boards against different wave types. If your new construction performs poorly in familiar surf conditions, it might be a sign to rethink certain design aspects.
"A smooth ride is more than just a desire; it’s the hallmark of a well-built surfboard that caters to your unique style."
Serious surfers often maintain a "board quiver." This collection illustrates a spectrum of performance options for various conditions. Testing and comparing not only allows you to appreciate your new creation but highlights what works and what doesn’t in surfboard construction. It lays a foundation for future designs, ensuring you engage in a cycle of improvement and innovation.
Common Challenges and Solutions
Building a surfboard can be a thrilling experience, yet it’s not without its hurdles. Recognizing and addressing the common challenges during the board-building process is essential for achieving optimal results. This section is more than just a list of problems; it highlights the intricacies involved in surfboard construction that builders must navigate.
Addressing Design Flaws
Design flaws can crop up during various stages of the surfboard building process. One common issue is the improper balance in dimensions or the outline that doesn't cater to the rider's style. If the nose is too wide and the tail too narrow, it could lead to unexpected performance issues on the waves.
Moreover, the rocker profile can also be a tricky area. A well-defined rocker can aid in maneuverability but if overdone, it will hinder speed. Builders often struggle between multiple design templates or styles that might fit their ideal vision. This all boils down to understanding how each design element impacts the board’s performance. Utilizing a foam mock-up before committing to the final shape can help. It gives you a tactile feel, allowing adjustments before any permanent changes are made.
It's also vital to engage with other surfers in the community or forums like reddit.com where ideas and critiques flow freely. Knowledge sharing can prevent some serious missteps in design that new builders might overlook.
Repairing Damage Post-Construction
Even with careful craftsmanship, surfboards can encounter wear and tear after hitting the waves. Whether it’s from rough landings or a careless bump on the car during transport, knowing how to properly repair damage is crucial. A small crack or ding, if left unattended, can expand and lead to more significant issues, like water intrusion.
The first step in repairing is assessing the damage. Use a fine-grit sandpaper to smooth out ragged edges, ensuring the surface is clean. For small dings, a simple epoxy resin can do the trick. Mix it as per the instructions on the package, then apply it to the area, ensuring it fills the crack entirely. For larger damages, like major punctures, you might need to place a patch of fiberglass cloth over the damaged area before applying resin. This method reinforces the structure, adding strength back to the board.
Remember that patience is key when it comes to repairs. Allow for adequate curing time as specified by the resin manufacturer; rushing this step can lead to subpar results. Keeping your surfboard in optimal condition will ultimately enhance its performance and longevity, ensuring it’s ready to ride those perfect waves every time you hit the waters.
Quick Tip: Always check the condition of your surfboard after each session. Early repairs can save you time and money down the line.
Engage with seasoned surfers or join workshops to enhance your repair skills. Each repair is a lesson, leading to a more refined technique in the long run. Taking the time to learn from each encounter will eventually pay off, giving you and your board a long-lasting relationship.
Personalizing Your Surfboard
Personalizing a surfboard is one of the most engaging aspects of the crafting journey. It’s not just about performance, but also about identity—infusing your essence into every corner of that board. When you create a custom surfboard, you’re signing up for a unique ride that reflects your very own style. This expression can come through in various ways: the artwork, the color scheme, and even the shapes you choose.
Artwork and Custom Graphics
Artwork on your surfboard isn’t just an aesthetic choice; it tells your story as a surfer. It's like painting a canvas that glides over waves rather than hangs on a wall. When thinkin about designs and graphics, people often pull inspiration from nature, surf culture, or even personal experiences.
- Choosing Your Theme: Consider themes that resonate with you. Whether it’s the vibrant hues of coral reefs or the stark contrast of black and white, your selection should encapsulate what surfing means to you.
- Techniques for Application: Some surfers opt for airbrushing, while others may prefer vinyl or stickers as a simpler route. Each technique carries its own vibe and durability, so weigh your options wisely.
Custom graphics often become conversations starters at the beach, allowing you to connect with fellow surfers who might appreciate your artistic flair. Plus, they can also serve as an emotional anchor, reminding you of waves you’ve conquered or times you’ve spent in the ocean.
Choosing the Perfect Color Scheme
Color schemes play a pivotal role in surfboard personalization. The palette you select can influence not only the board's attractiveness but also its perceived performance. Some colors absorb heat, which may affect the board's temperature when left in the sun, while lighter colors might reflect light but not offer as much warmth.
- Warm vs. Cool Tones: Warm colors, such as reds and oranges, can evoke energy and vitality; while cool colors like blues and greens are often reminiscent of calming ocean vibes. Think about what emotional response you want from both yourself and those around you.
- Consider Visibility: It’s equally crucial to ensure your board stands out in the water. A brightly colored board can make you more visible to other surfers and boaters, which can enhance safety.
In summary, personalizing a surfboard is about more than just looks; it's a significant part of building a relationship with your craft. As you ride the waves, the colors and designs telling your story will be evident to everyone. This connection transforms not just your surfing experience but also creates a deeper appreciation for the journey of crafting the perfect wave rider.
Handling and Maintenance of Your Surfboard
Taking care of your surfboard is not merely a chore; it’s an integral part of ensuring its long-lasting performance and appearance. The art of handling and maintenance extends well beyond just ensuring a clean board. It embodies a set of practices that, when adopted diligently, can enhance your surfing experience considerably. From prolonging the lifespan of your board to preserving its aesthetic appeal, proper care goes a long way.
Cleaning and Waxing
Let’s face it, surfboards can take quite a beating. Sand, saltwater, and other elements can accumulate on the surface, dulling its shine and potentially affecting performance. Cleaning your board regularly is crucial. A simple rinse after each session goes a long way; just grab a hose, hit it with some cool water, and rinse off all that pesky sand and salt.
Beyond a quick rinse, you should dive deeper into a thorough clean every so often:
- Use mild soap: A gentle dish soap mixed with water can help break down grime. Avoid harsh chemicals as they can damage the finish and overall integrity of your board.
- Soft cloth or sponge: Employ a non-abrasive cloth or sponge when cleaning. This avoids scratches while still getting into the tiny crevices.
- Waxing: After cleaning, it’s time to get to work on your board’s traction. Wax builds a grip that’s essential during rides. Make sure to remove old wax with a wax comb before applying new layers. Be sure to apply evenly so it doesn't become more slippery in sections.
Keeping your board clean doesn’t just preserve its visual appeal; it also maintains its functionality. A well-maintained surfboard not only looks sharper, but also performs better in water, allowing you to slice through waves like a hot knife through butter.
Storage Considerations
Storage is another pivotal aspect of surfboard upkeep. How you store your board can dramatically affect its condition over time. Consider these tips for optimal storage:
- Avoid direct sunlight: Sunlight can warp and discolor your board. Opt for a cool, shaded spot if possible.
- Use a board bag: Investing in a good quality board bag provides padding and protection from dings during transport and storage. It’s like a cozy blanket for your wave-riding companion.
- Vertical storage: If possible, store your board vertically. This minimizes pressure on the fins and allows even airflow around it.
"A keen eye for maintenance can extend your board's life and enhance every ride you take."
Lastly, while it may seem tempting to leave your board propped up in a corner or leaned against a wall, that's asking for trouble. It can easily get knocked over or damaged. As you nurture your board, it rewards you with enhanced performance and durability, translating into countless memorable surfing adventures.
By paying attention to the details of handling and maintenance, you're not just caring for a surfboard; you're investing in your journey as a surfer.
Ending: Reflecting on the Craft
Building your own surfboard invites an unparalleled journey that transcends mere recreation. It fosters a deep relationship with the ocean, engaging the body and mind in concert. This exploration has not only illuminated the intricacies of surfboard creation but has also served to emphasize the vital connection between surfboard design and personal expression. Customization stands at the forefront of this narrative, acting as a bridge between the builder's vision and their surfing aspirations.
The satisfaction stemming from creating something tailored to your own specifications cannot be overstated. When one takes the plunge into customizing their board, they step beyond the norm, pouring their personality and preferences into every angle and curve. This artistic endeavor transforms the act of surfing into an experience that is profoundly personal.
The Joy of Custom Creation
Custom creation opens the door to explore your unique style. Each board tells a story — from the shape you select to the colors and artwork you embed onto its surface. This aspect of crafting offers numerous benefits:
- Expression of Identity: A surfboard is not just equipment; it’s a canvas rich with possibilities. Whether it’s a minimalist aesthetic or a vibrant explosion of color, your board speaks volumes about who you are.
- Tailored Performance: Different shapes and designs affect how a surfboard behaves in water. Your choice of fins, rocker, and volume can cater to your specific surfing style or the kind of waves you prefer, unlocking enhanced performance.
- Sense of Accomplishment: There’s a tangible satisfaction that arises from building something with your own hands. Seeing an idea transform into a crafted object generates pride and a sense of achievement that no store-bought board can replicate.
In the end, every stroke of sandpaper and touch of resin brings you closer to a product that is an extension of yourself in the water.
The Impact of Surfboard Design on Experience
As we wrap up this investigation into surfboard building, one cannot overlook how critical design is to the overall surfing experience. What individuals often pedal past is the fact that each aspect of a surfboard is meticulously engineered to enhance ride quality.
- Wave Dynamics: The design influences how the board interacts with waves. A fish tail might glide swiftly through small swells, while a tapered tail can connect better with powerful breaks.
- Personal Comfort: The ergonomics of the board — including size and weight — play into how comfortable a rider feels on the board, affecting everything from paddling to duck diving.
- Connection to Nature: A thoughtfully designed surfboard resonates with the ocean’s energy, allowing you to feel every ripple and swell. Tuning into this connection can elevate a rider’s experience, transforming a routine surf session into an exhilarating dance with nature.
Thus, the art of surfboard design does not merely reside in aesthetics but is a core element of every surfer’s relationship with the ocean.