The Impact of CNC Machines on Surfboard Production
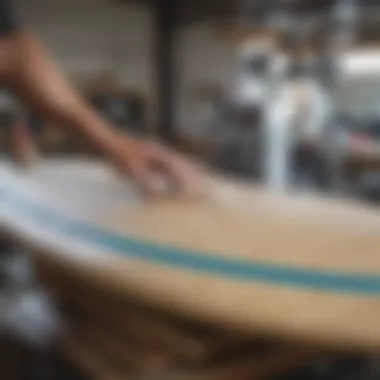
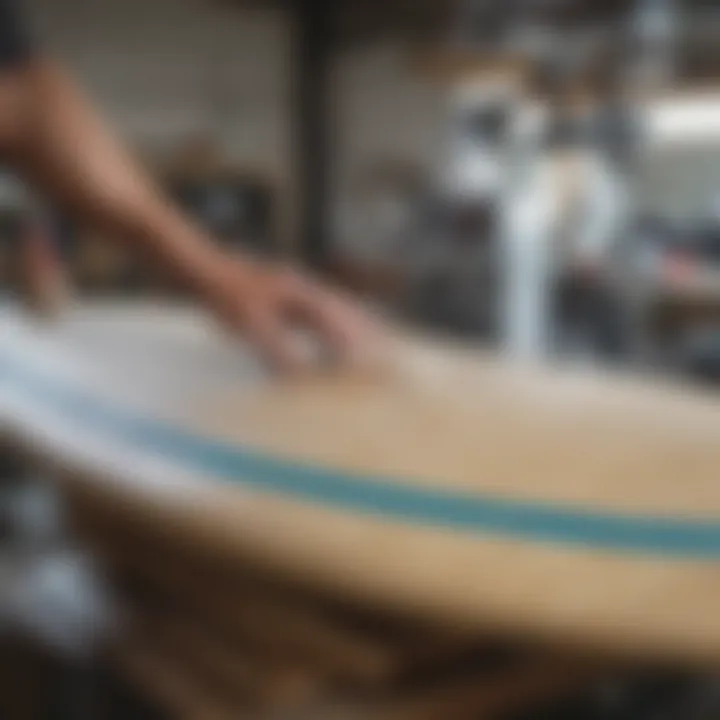
Intro
In recent years, the surfboard manufacturing industry has seen remarkable advancements, thanks to the advent of CNC machines. These high-precision tools have revolutionized the way surfboards are produced, offering endless possibilities and improved efficiencies. The integration of this technology allows manufacturers to create unique, tailored designs with a level of accuracy that was previously unattainable. This article will delve into the several ways CNC machines influence surfboard production, enhance performance, and shape the future of the watersport industry.
Tips and Techniques
Beginner Tips for Watersports
For those new to surfing, understanding the intricacies of surfboard design is key. CNC machines play a significant role in shaping surfboards that cater to various skill levels and styles. Here are some fundamental tips to consider as you explore:
- Choose the Right Shape: Beginners should generally opt for wider and thicker boards, which provide more stability.
- Understand the Materials: Familiarize yourself with foam types used in surfboard cores. EPS and polyurethane are the most common choices, with CNC machines significantly contributing to the shaping process of both.
- Embrace Customization: Donβt hesitate to explore custom designs through CNC technology. They allow for specific dimensions tailored to your height and weight, enhancing your surfing experience.
Advanced Techniques for Mastery
Once you gain confidence on the waves, itβs time to elevate your skills. Advanced surfers will appreciate how CNC machines facilitate deeper customizations and balance. Hereβs what to keep in mind:
- Board Performance Profiling: Engage with shapers who utilize CNC machines to profile your board accurately for differing conditions.
- Fin Customization: The accuracy of CNC machining allows for finessed fin placements, crucial for turning and maneuverability in advanced surfing.
- Material Selection: Experiment with different foam densities combined with resin types to suit various wave conditions and personal preferences.
Safety and Gear
Essential Safety Practices
Regardless of your level of experience, safety in watersports should be a top priority. CNC-machined boards are designed with user safety in mind, yet itβs essential to remember these key practices:
- Wear a Leash: Always attach a leash to your board to prevent it from drifting away.
- Familiarize Yourself with the Environment: Take note of local tides, currents, and any submerged hazards in the area.
- Stay Hydrated and Protect Yourself: Apply a strong sunscreen and drink plenty of water when spending hours on the beach.
Gear Reviews and Recommendations
Having the right gear is crucial for an enjoyable surfing experience. Some essential items include:
- Surfboard Bag: Protect your CNC-shaped board with a padded bag to prevent dings and scratches.
- Wetsuit: Invest in a high-quality wetsuit based on the water temperature of your surfing location. Look for materials that utilize insulation and flexibility.
- Wax: A good traction pad or wax helps to keep your grip secure on the board, enhancing overall control.
"CNC machines have not just changed the production process, but theyβve redefined the standards of surfboard performance, giving surfers a new edge."
The future of surfboard production is undeniably intertwined with CNC technology. As manufacturers continue to innovate, we can expect to see even more tailored solutions that cater to both new and experienced surfers alike. By understanding these dimensions from a production perspective, enthusiasts and professionals can make informed choices about their surfboards and gear.
Preamble to CNC Technology in Surfboarding
The intersection of surf culture and advanced technology heralds a new era in surfboard manufacturing. CNC, or Computer Numerical Control, machines are drastically changing how surfboards are designed and produced. This technology doesn't just add efficiency; it brings a level of precision and customization that's hard to achieve through traditional methods.
Definition of CNC Machines
CNC machines operate through a series of programmed commands that control tools to create physical objects from raw materials. Specifically for surfboarding, CNC routers, and laser cutters are the main players. These machines can cut foam, wood, or composites with exceptional accuracy. This means that a surfboard can be tailored to the user's exact specifications, from its dimensions to intricate designs.
"In the world of waves, aligning your equipment to your personal needs is keyβCNC machines make that possible!"
With the ability to reproduce designs with pinpoint accuracy, CNC machines facilitate a streamlined production process, allowing manufacturers to create multiple boards that maintain consistency in quality. Simply put, they make the impossible possible when it comes to producing performance-oriented surfboards.
History of Surfboard Manufacturing
Surfboard manufacturing has roots tracing back to ancient Polynesian cultures, where large wooden boards were crafted by hand. These artisans relied heavily on natural materials and traditional techniques. As surfing gained popularity in the 20th century, particularly after World War II, the materials and manufacturing processes evolved significantly.
The introduction of foam cores and fiberglass marked a pivotal shift. However, the process remained labor-intensive and limited in scalability. Surfboard shapers were artists, hand-crafting each board in workshops, often resulting in unique but inconsistent products. The move towards automated production lines began in the latter part of the 20th century, but it was the advent of CNC technology that truly revolutionized the game.
Todayβs manufacturers blend these time-honored crafting techniques with cutting-edge CNC technology. This amalgamation not only respects the heritage of surfing but also meets the demands of modern performance standards. High-level surfboard makers can create boards that are not only visually stunning but also optimized for speed and maneuverability. As the industry continues to adapt, the role of CNC machines will undeniably become even more significant.
Benefits of CNC in Surfboard Production
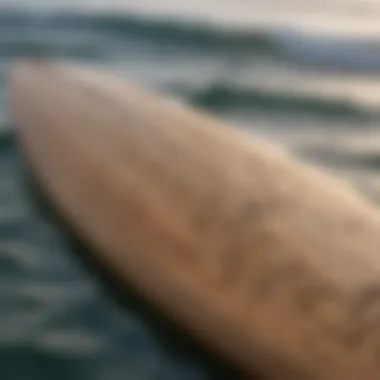
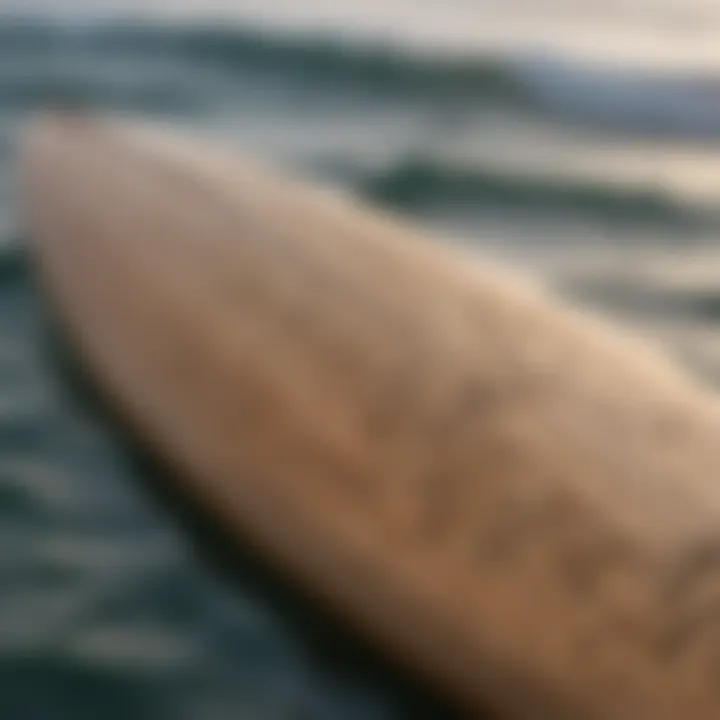
The integration of CNC machines into surfboard production has been a game changer, shifting the paradigm of how surfboards are conceived and crafted. The precision and efficiency offered by these machines allows producers to push the boundaries of design and execution in ways that were inconceivable with traditional methods. Delving deeper into this, several specific benefits stand out, providing a distinct edge in both the artistic and practical elements of surfboard manufacturing.
Precision and Consistency
Perhaps the most critical aspect of employing CNC machines in surfboard production is the precision they deliver. A CNC machine operates using computer-generated designs, leading to an accuracy level that can be off by mere microns. This level of precision is paramount in surfboard crafting, where even slight deviations can affect performance. If you think about a surfboard's shape and contours, any inconsistencies can result in subpar performance in the water.
The fact that CNC machines maintain this level of consistency across production runs means that whether it's the first board or the hundredth, they all meet high standards. This repetitive excellence reduces the need for rework and adjustment, streamlining the entire production process.
"In surfboard production, a consistent shape isn't just desirableβit's essential for performance. CNC machines take guesswork out of the equation."
Customization Options
Customization has become the name of the game in many industries, and surfboarding is no exception. With CNC technology, manufacturers can offer individualized shapes, sizes, and designs tailored to each surfer's unique preference. For instance, an experienced surfer might want a narrower tail or a different rocker, which can be easily rendered through CNC programming.
The beauty of CNC technology lies in its ability to accommodate diverse preferences without incurring significant time or cost penalties. This level of customization also extends to graphics and aesthetics, as surfers can personalize their boards with specific patterns or colors, making each piece a work of art. The flexibility to switch from one design to another with a few clicks greatly enriches the surfboard community.
Time Efficiency in Production
Time is often an elusive luxury in production environments, and CNC machines help reclaim it. Unlike traditional hand-shaping, which can be lengthy and a tad unpredictable, CNC machines require less direct human intervention once programmed. This results in quicker turnaround times.
From the initial design phase to final product, the CNC process simplifies workflows significantly. Tasks that used to take days can now be accomplished in hours. Moreover, the capability to produce multiple boards simultaneously means manufacturers can keep up with growing demand without sacrificing quality.
Manufacturers who adopt CNC technology not only satisfy current customers more effectively but also position themselves strategically for future growth. Speed without the loss of quality is a critical competitive advantage in todayβs market.
With these benefits in mind, it's clear that CNC machines have a significant role to play in the evolution of surfboard manufacturing, influencing everything from design deepness to market responsiveness.
Types of CNC Machines Used in Surfboard Production
In the realm of surfboard production, CNC machinery represents a pivotal advancement. These machines streamline manufacturing, elevate precision, and cater to unique user preferences. Understanding the types of CNC machines utilized is essential, as it unveils the diversity of options available, each serving distinct functions that contribute to the superior quality of surfboards.
Router CNC Machines
Router CNC machines are perhaps the heavyweights in surfboard crafting. These machines primarily function through spinning bits that cut into solid materials, making them well-suited for shaping foam cores and intricate designs. The capability of a router CNC to execute complex curves and multi-dimensional shapes cannot be overstated. When used effectively, one can achieve the sleek aesthetics that many surfers appreciate.
Moreover, router CNCs are incredibly user-friendly. Many come with intuitive software that allows artisans, from beginners to seasoned shapers, to design and modify features quickly. For anyone keeping an eye on production efficiency, this ease translates to significantly reduced time between prototype and finished product.
"CNC routers democratize design. It makes it possible for newcomers to enter the surfboard scene, altering traditional methods while retaining creative expression."
Furthermore, the versatility of router CNC machines means they can handle a variety of materials, whether itβs different types of foam, wood, or even composite materials. Such a range allows surfboard manufacturers to experiment with various performance metrics and aesthetics.
Laser Cutters
Laser cutters hold a crucial role in the production line, primarily for their precision in cutting and engraving. Unlike router CNCs, which remove material by cutting, laser technology uses a focused beam of light to slice through the material with uncanny accuracy. This means that fins, intricate logos, or custom lettering can be applied with an elegance that's hard to match through traditional methods.
What's more, laser cutters can work with a broad palette of materials, including epoxy and some woods, expanding the creativity available to surfboard designers. This precision cuts down on waste, contributing to a leaner production cycle and more environmentally responsible practices. In an industry increasingly focused on sustainability, the ability of laser technology to create less material waste is a significant advantage.
These machines particularly shine in the customization arena. With laser cutters, manufacturers can easily personalize designs or collaborate with artists to achieve one-off pieces that resonate with individual tastes. So whether someone is chasing performance or looking to make a statement on the waves, laser-cut elements can augment the overall appeal.
Both router CNC machines and laser cutters have their unique strengths, but together, they represent a comprehensive approach to surfboard production that merges artistry with technology.
Material Selection for CNC Surfboards
Material selection plays a pivotal role in the production of CNC surfboards. The choice of materials not only influences the manufacturing process, but also impacts the board's overall performance, durability, and rider experience. In this section, weβll delve into the common materials used in surfboard construction and uncover how these choices resonate throughout the surf industry.
Common Materials in Surfboard Construction
It all starts with the foundation. When it comes to crafting surfboards, several materials have taken center stage:
- Polyurethane (PU): A traditional favorite, PU foam is lightweight and offers an excellent balance between strength and flexibility. It's widely used in custom surfboards for its responsive nature, making it a go-to among many shapers.
- Epoxy Resin: Known for its durability and resistance to dings, epoxy resin is often paired with expanded polystyrene (EPS) foam. This combination generally results in a lighter board that maintains integrity even in harsh conditions.
- EPS Foam: The lightweight alternative to PU, EPS foam is often chosen for its buoyancy and performance attributes, especially in high-speed surf scenarios.
- Wood: While somewhat unconventional, wooden surfboards are making a comeback, with unique aesthetic appeal and sustainable sourcing. They often involve CNC for precision cutting, highlighting the modern adaptation of traditional methods.
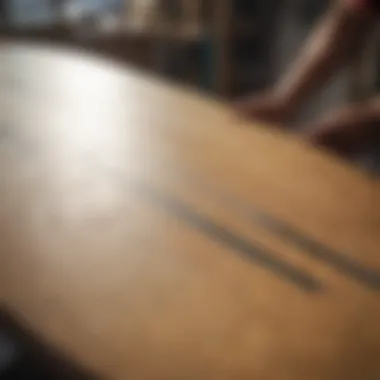
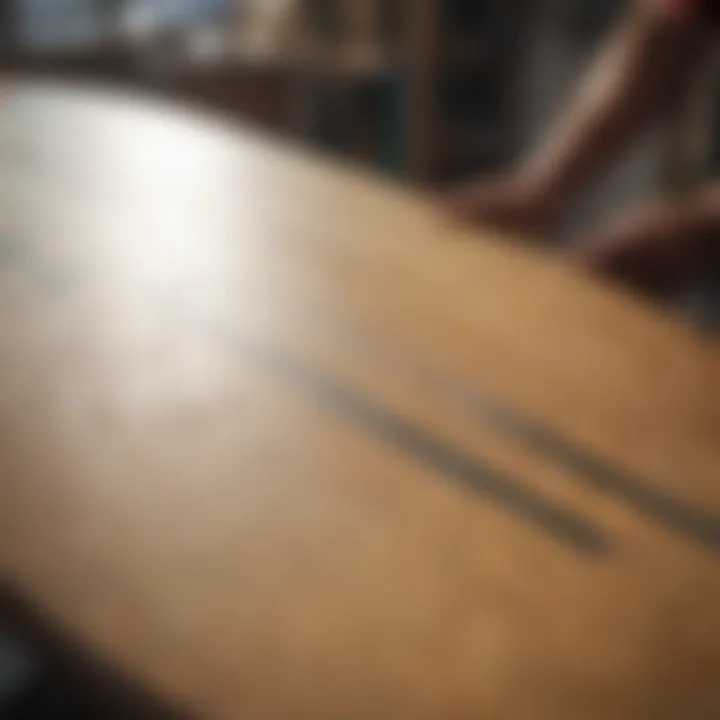
Overall, choosing materials isn't merely about preference; it's about engineering specific attributes that align with what surfers look for in performance.
Impact of Material Choices on Performance
The interplay between materials and a surfboard's performance is profound, affecting everything from maneuverability to wave handling. Here are some key considerations when selecting materials:
- Strength-to-Weight Ratio: Lightweight boards enhance mobility; however, they must maintain enough durability to withstand the rigors of regular surfing. For instance, a board made of EPS with epoxy resin often delivers high performance while keeping weight down.
- Flexibility and Rigidity: Boards that feature a blend of materials can offer diverse flex patterns. A PU core with a fiberglass layer can provide both required stiffness yet enough flex to allow for dynamic turns.
- Water Resistance: The choice between different resins can dictate how water impacts the lifetime of a surfboard. Epoxy, for example, often serves better in this aspect compared to standard polyester resins.
"The material selection for a surfboard is not just a factor of construction; itβs an entire system that embodies the essence of the ride."
- Environmental Considerations: With increasing awareness around sustainability, many manufacturers are opting for eco-friendly materials. Options such as bio-resins hold promise for reducing environmental impact, allowing surfers to ride with a clear conscience.
Design Considerations for Surfboards with CNC Technology
When it comes to crafting surfboards, the integration of CNC technology offers a new horizon of design possibilities. This section focuses on understanding critical design aspects, primarily aerodynamics and hydrodynamics, followed by customization based on user requirements.
Aerodynamics and Hydrodynamics
The principles of aerodynamics and hydrodynamics are at the core of any surfboard design. These concepts are not just scientific jargon; theyβre essential for how the board performs on waves. Simply put, aerodynamics deals with the interaction between objects and air, while hydrodynamics focuses on objects in water.
By utilizing CNC technology, manufacturers can mold surfboards with precise contours that optimize both airflow and water flow over the surface. This is crucial because the shape of a board can significantly influence speed, maneuverability, and stability. For instance, a board with a sleek, narrow profile will slice through the water more efficiently, creating less drag. In contrast, a wider board with rounded edges can provide better buoyancy, allowing surfers to float and catch waves more effectively.
Moreover, CNC machines can replicate these ideal shapes consistently, ensuring that every board meets specific performance standards. Custom designs can be generated, tweaking dimensions to accommodate various surf styles and preferences. This adaptability is what sets CNC technology apart from traditional methods, where much of the shaping relies on manual skill and experience.
"Understanding the intricate dance between aerodynamics and hydrodynamics is like learning to read the waves. Mastery of these aspects can lead to an incomparable surfing experience."
Adjusting Design Based on User Preferences
Not all surfers are cut from the same cloth; their preferences can vary wildly depending on skill level, surfing style, and even personal aesthetic choices. This where CNC technology gets interesting. Given its precision, users can enjoy boards tailored to their unique preferences.
A beginner might benefit from a wider, more stable board that provides greater balance, while an experienced rider may prefer a board with a narrower tail for sharper turns. By leveraging the flexibility offered by CNC milling, manufacturers can accommodate these unterschiedlich requests seamlessly. CNC programming allows designers to input specific parameters based on user feedback which can result in unique modifications.
A few key elements to consider in this process include:
- Tail Shape: The tail design influences how the board reacts when taking off. Different shapes can enhance or hinder performance.
- Thickness: A thicker board can provide additional buoyancy, ideal for paddling and catching small waves, but can also inhibit performance in larger swells.
- Graphics and Personalization: Beyond functionality, CNC allows for intricate graphics, giving every board a personal touch that reflects individual style.
Moreover, the collaborative process between manufacturers and users enriches the design experience. Surfers can communicate their specific needsβperhaps they want a little extra width or a particular artwork on their board. With CNC technology, adjustments can be made efficiently, providing a truly customized riding experience.
CNC Machine Operation in Factories
The operation of CNC machines in surfboard production is a vital element that can make or break the efficiency and quality of the manufacturing process. Understanding how these machines are set up, programmed, and troubleshooted is essential for any surfboard manufacturer looking to leverage the benefits of CNC technology. The intricate dance of machinery and programming allows for the creation of surfboards that can meet a diverse range of performance needs.
Setup and Programming of CNC Machines
Setting up a CNC machine is akin to laying down the foundation before building a house. This process starts with selecting the right machine for the task. Various models might cater best to different surfboard types, whether it's a shortboard or a longboard. Generally, the setup involves securing the blank surfboard material firmly on the machine bed, ensuring that the alignment is spot on. Even a millimeter off can lead to disastrous results.
Once the material is in place, programming comes into play. This phase requires knowledge of CAD (Computer-Aided Design) software to create a digital model of the surfboard. The CNC machine reads this model to understand how to cut and shape the board. Accordingly, precision is paramount. If there are discrepancies in the design input, the machine might produce a sub-standard board that fails to meet the specifications desired by the end user.
A few common elements in programming include setting the correct tool paths, adjusting feed rates, and ensuring the right tools are selected for the operation. Itβs also wise to simulate the machining process in software before actual production begins. This step saves time and minimizes material waste. Coping with the ever-evolving demands of surfers requires an agile approach in this phase; adapting design inputs swiftly while keeping the setup intact speaks volumes about a manufacturer's capability.
Troubleshooting Common Issues
Despite meticulous planning and execution, challenges may still crop up during CNC operations. Understanding common issues and their solutions can significantly reduce downtime and maintain productivity.
First off, one may encounter software glitches or crashes. When this happens, it can leave the machine stalling mid-process, and thatβs no good. Regular software updates and ensuring compatibility can stave off many of these problems.
Next, consider mechanical issues which can range from misaligned tools to broken bits. For instance, if the machine skips a cut, it might be due to dull tools or improper calibration. Keeping spare parts handy can be a lifesaver. Being married to a scheduled maintenance routine assures that machines are running at their best.
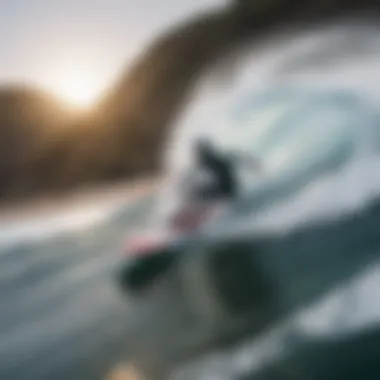
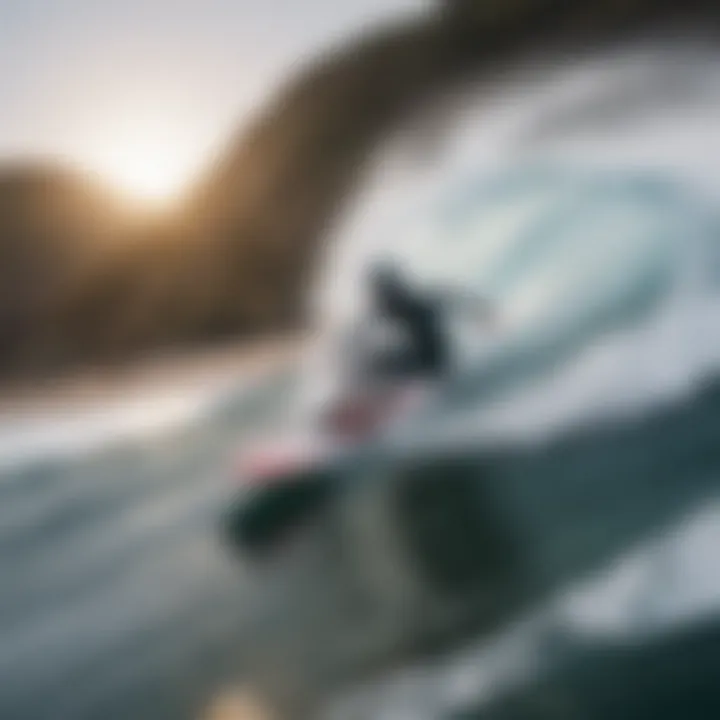
Finally, the human element canβt be brushed aside. An operatorβs inexperience might lead to oversight in programming or incorrect material setup. This highlights the importance of proper training and ongoing education for anyone manning the machine.
βInvesting in knowledgeable personnel is as crucial as having the best machinery.β
These troubleshooting methods and operational tactics are part and parcel of CNC machine operation in surfboard production. By mastering these, manufacturers not only enhance their production capabilities but also contribute to the overall quality of the surfboards they produce.
Continued investment in training and technology will keep the operation efficient and aligned with evolving surfboard design trends.
Case Studies of Successful Surfboard Manufacturers
Examining the experiences of specific surfboard manufacturers provides valuable insight into how CNC technology has reshaped the industry. By focusing on tangible examples, readers can grasp the real-world applications of CNC machines in surfboard production. This section will shed light on how various manufacturers harness CNC capabilities to deliver superior products, pushing them towards success in a competitive market.
Case Study: Innovative Surfboard Makers Using CNC
One prime example is Firewire Surfboards, a company known for its advanced manufacturing techniques using CNC machines. They have integrated computer-controlled equipment to streamline their production, enabling them to produce high-quality surfboards efficiently. The precision of CNC machines allows Firewire to create complex designs while ensuring uniformity across their products. This consistency in quality has garnered a loyal following among surfers who crave performance and reliability on the water.
Another noteworthy mention is Lost Surfboards. Their ability to customize shapes quickly via CNC has significantly shortened development times. Using these machines, they can easily morph designs based on feedback from professional surfers, leading to products that resonate with the specific needs of their audience. The rapid prototyping that CNC allows ensures that new ideas can be tested without hefty time investments.
Moreover, companies like Rinse have embraced sustainable practices by utilizing CNC technology for wood surfboards. While traditional methods often involve extensive material waste, CNC machining optimizes cuts, resulting in better use of resources. Rinse illustrates that eco-friendliness can go hand-in-hand with innovation and performance, tapping into a niche market of environmentally conscious surfers.
Comparative Analysis of Traditional vs. CNC Methods
The contrast between traditional surfboard shaping and CNC machining cannot be overstated. Traditionally, surfboards were hand-shaped, a painstakingly slow process requiring years of experience to perfect. While this method allows for artistic creativity and unique craftsmanship, it's not always consistent in quality. Hands-on shaping has its charm, but when it comes down to precise measurements and replicable results, CNC technology finds its strength.
- Consistency: With CNC machines, each board produced adheres to exact specifications. This level of precision is hard to achieve through hand shaping.
- Speed: Traditional shaping methods can take days, whereas CNC machines can churn out designs in hours, allowing manufacturers to keep pace with market demand.
- Customization: CNC enables quick alterations in designs based on user preference, something thatβs more cumbersome with traditional methods.
Yet there are elements of traditional craftsmanship that CNC cannot fully replicate. The human touch that goes into hand shaping involves sensory feedback and a personal artistry that machines lack. Some premium brands continue to offer limited-edition boards shaped by skilled artisans, creating a high-value item appreciated by collectors and enthusiasts.
Future Trends in Surfboard CNC Machining
As the surfing world continues to embrace innovation, the integration of CNC technology remains at the forefront of surfboard production. Understanding the future trends in surfboard CNC machining provides insight into how the industry will evolve, influence design, and meet the demands of both amateur surfers and seasoned professionals. This evolution not only enhances performance but also opens doors to new materials and methods of crafting boards.
Embracing these trends can lead to significant benefits including improved efficiency, enhanced creativity in design, and heightened sustainability practices. Let's dive into some of the pivotal shifts on the horizon.
Automation and Robotics in Surfboard Production
Automation is setting the stage for a new era in surfboard manufacturing. By integrating robotic systems, production lines can ramp up efficiency and reduce human error. These automated machines are capable of performing complex tasks with precision, leading to remarkably consistent results.
For instance, manufacturers are increasingly adopting robotic arms for tasks such as shaping, sanding, and finishing boards. This shift minimizes the manual workload on workers, allowing skilled artisans to focus on more intricate design elements that require a human touch. Here are several key points to consider:
- Increased Output: The use of automation can drastically speed up the production process. Instead of taking weeks, creating boards can take days, or even hours.
- Reduced Waste: Enhanced precision reduces material overspending, a significant concern in traditional methods. CNC machines can cut materials with near-zero waste due to their programmed accuracy.
- Custom Features: Robotic systems can effortlessly integrate unique design features that cater to individual surfer preferences, thereby combining mass production with personalization.
- Consistency in Quality: Automation ensures that each board is manufactured to the same high standard, which is often difficult to achieve manually.
"The future of surfing is not just the waves but also the technology that crafts the waves we ride."
Sustainability Initiatives in Manufacturing
As the surfing community becomes increasingly aware of environmental impacts, sustainability initiatives are becoming essential in surfboard production. CNC machines are significantly contributing to these efforts. By optimizing manufacturing processes, companies can utilize eco-friendly materials more effectively, reduce energy consumption, and minimize waste.
Key strategies for achieving sustainability include:
- Use of Recyclable Materials: Innovations in materials, such as bio-resins and recycled foams, are gaining traction. CNC technology ensures that these materials can be used efficiently, maintaining performance standards while being kinder to the planet.
- Energy-efficient Machines: Modern CNC machines are designed to consume less power compared to older models. This transition not only cuts costs but also reduces the carbon footprint of the manufacturing process.
- Local Production: With advanced CNC technology, local manufacturers can produce surfboards closer to the end user, reducing transportation emissions. This idea promotes a more localized surfing culture and community.
- Design for Disassembly: Crafting boards that can be easily disassembled at the end of their life cycle allows for recycling and disposal that returns valuable materials back into the production cycle.
Staying ahead of these trends not only strengthens the environmental integrity of the surfboarding community but also aligns with a growing consumer preference for sustainable products.
End
The integration of CNC machines into surfboard production has transformed how surfers and manufacturers approach the sport. Understanding this technology allows both athletes and professionals to appreciate the intricacies of how modern surfboards are crafted. CNC not only streamlines the manufacturing process but also ensures a degree of precision that traditional handmade boards may not achieve.
Summarizing Key Insights
The significant takeaways from this exploration are crucial for anyone involved in the world of surfboarding:
- Precision and Consistency: CNC machines eliminate human error, providing uniformity across mass-produced boards. This can lead to improved performance, as surfers can rely on the design specifications.
- Customization Options: With CNC technology, shapers can create unique designs tailored to individual preferences. Surfers can optimize performance based on their skill level and surfing style, breaking away from the one-size-fits-all approach.
- Time Efficiency in Production: CNC machines drastically reduce the production timeline, enabling manufacturers to meet growing demand without sacrificing quality.
- Innovation and Technology: The evolution of CNC technology has opened the door for new materials and design possibilities, pushing the boundaries of what's achievable in surfboard performance.
- Sustainability Considerations: As the surf industry begins to focus on environmental impact, CNC machines can aid in efficient material use, reducing waste.
"The future of surfboard manufacturing is not only about efficiency and customization but also about aligning with sustainability goals, ensuring that the beauty of the ocean is preserved for future generations."